Post by account_disabled on Mar 14, 2024 0:28:29 GMT -5
Consideration is product efficiency improvements resulting from new technologies. If product technology (in tens of operating energy or resource consumption) changes rapidly it might be advantageous to upgrade products (meaning change and replace) more often. Alternately, if product technology evolves slowly, there may be little advantage, from a consumption angle, to upgrading. The tipping point is with respect to embodied energy in the product.
Julian Allwood, who’s been mentioned before in this blog, covers the tradeoff in his book Allwood and Cullen, UIT, Cambridge, . There are two distinct strategies CG Leads depending on whether or not the product has “high embodied energy” or “low embodied energy”.
Recall that embodied energy is the energy (and resources with their energy footprints) required to manufacture the product. Products with high embodied energy and low energy in use are candidates for replacement less often with technology enhancements while product with low embodied energy and high energy in use with improving efficiency are candidates for replacement more often as seen below.
The strategy can have a big impact on the cumulative emissions (as from the energy) over the life
cycle of the product. This was the issue we discussed some time ago with respect to the “cash for clunkers” program as part of the recovery – it would be advantageous, from an environmental angle, to replace an old car with a newer car only if the newer car had sufficiently better fuel economy to offset over its life the embedded energy of the vehicle it was replacing plus save fuel.
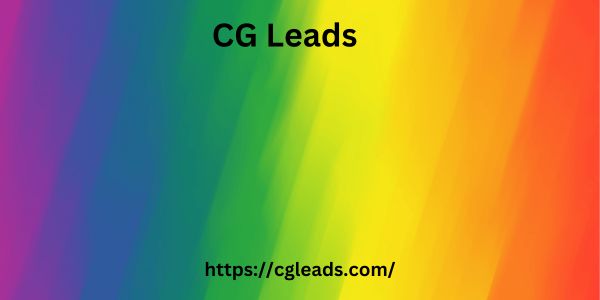
Enough to consider for the moment. I’ll pursue this more with respect to frugal engineering and green in the next article.
David Dornfeld is the Will C. Hall Family Chair in Engineering in Mechanical Engineering at University of California Berkeley. He leads the Laboratory for Manufacturing and Sustainability (LMAS), and he writes the Green Manufacturing blog.
A product life: an infant mortality period (early failure)
with a decreasing failure rate, then a normal life period (also known as “useful life”) with a low, relatively constant failure rate, and ending up with a wear-out period of accreted failure exhibiting an increasing failure rate. Engineers try to reduce failures at each stage of product life by efforts such as “burn-in” or running the product for some time to catch early failures or other tests to attempt to screen out infant mortality failures. Design and manufacturing choices can reduce (or increase!) failures at any stage – depending on quality of components and design and production.
Julian Allwood, who’s been mentioned before in this blog, covers the tradeoff in his book Allwood and Cullen, UIT, Cambridge, . There are two distinct strategies CG Leads depending on whether or not the product has “high embodied energy” or “low embodied energy”.
Recall that embodied energy is the energy (and resources with their energy footprints) required to manufacture the product. Products with high embodied energy and low energy in use are candidates for replacement less often with technology enhancements while product with low embodied energy and high energy in use with improving efficiency are candidates for replacement more often as seen below.
The strategy can have a big impact on the cumulative emissions (as from the energy) over the life
cycle of the product. This was the issue we discussed some time ago with respect to the “cash for clunkers” program as part of the recovery – it would be advantageous, from an environmental angle, to replace an old car with a newer car only if the newer car had sufficiently better fuel economy to offset over its life the embedded energy of the vehicle it was replacing plus save fuel.
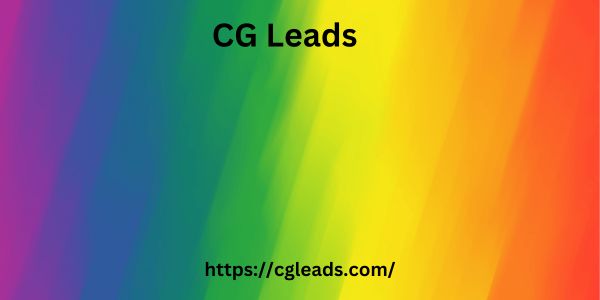
Enough to consider for the moment. I’ll pursue this more with respect to frugal engineering and green in the next article.
David Dornfeld is the Will C. Hall Family Chair in Engineering in Mechanical Engineering at University of California Berkeley. He leads the Laboratory for Manufacturing and Sustainability (LMAS), and he writes the Green Manufacturing blog.
A product life: an infant mortality period (early failure)
with a decreasing failure rate, then a normal life period (also known as “useful life”) with a low, relatively constant failure rate, and ending up with a wear-out period of accreted failure exhibiting an increasing failure rate. Engineers try to reduce failures at each stage of product life by efforts such as “burn-in” or running the product for some time to catch early failures or other tests to attempt to screen out infant mortality failures. Design and manufacturing choices can reduce (or increase!) failures at any stage – depending on quality of components and design and production.